An alloy of chromium, cobalt and nickel has just given us the highest fracture toughness ever measured in any material on earth.
It has exceptionally high strength and ductility, resulting in what a team of scientists has called “outstanding damage tolerance.”
Furthermore—and counterintuitively—these properties increase as the material gets colder, suggesting interesting potential for applications in extremely cryogenic environments.
“When you design structural materials, you want them to be strong, but also stretchy and break-resistant,” says metallurgist Easo GeorgeGovernor’s Chair for Advanced Alloy Theory and Development at Oak Ridge National Laboratory and the University of Tennessee.
“Usually it’s a compromise between those qualities. But this material is both, and instead of becoming brittle at low temperatures, it hardens.”
Strength, ductility and toughness are three properties that determine how durable a material is. The strength describes the resistance to deformation. And ductility describes how malleable a material is. These two properties contribute to its overall toughness: breaking strength. Fracture toughness is the resistance to further fracture in an already fractured material.
George and his colleague, mechanical engineer Robert Richie of Berkeley National Laboratory and the University of California, Berkeley, have spent some time working on a class of materials known as high entropy alloys, or HEAs. Most alloys are dominated by one element, mixed with small amounts of others. HEAs contain elements mixed in equal proportions.
One such alloy, CrMnFeCoNi (chromium, manganese, iron, cobalt and nickel), was subsequently the subject of intensive studies scientists noticed that its strength and ductility increase at liquid nitrogen temperature without sacrificing toughness.
A derivative of this alloy, CrCoNi (chromium, cobalt and nickel), also showed exceptional properties. So George and Ritchie and their team cracked their knuckles and set out to push it to its limits.
The previous experiments on CrMnFeCoNi and CrCoNi were carried out at liquid nitrogen temperatures up to 77 Kelvin (-196°C-321°F). The team has pushed it even further, to liquid helium temperatures.
The results were more than impressive.
“The toughness of this material at liquid helium temperatures (20 Kelvin, [-253°C, -424°F]) is as high as 500 megapascals square root meter”, Ritchie explained.
“In the same units, the toughness of a piece of silicon is one, the aluminum cell in passenger planes is about 35, and the toughness of some of the best steels is about 100. So 500, that’s an amazing number.”
To find out how it works, the team used neutron diffraction, electron backscatter diffraction, and transmission electron microscopy to study CrCoNi down to the atomic level when fractured at room temperature and in extreme cold.
This involved breaking the material and measuring the stress required to grow the fracture, and then looking at the crystalline structure of the samples.
Atoms in metals are arranged in a repeating pattern in three-dimensional space. This pattern is known as the crystal lattice. The repeating components in the lattice are known as unit cells.
Sometimes boundaries are created between deformed and non-deformed unit cells. These boundaries are called dislocations, and when a force is applied to the metal, they move, allowing the metal to change shape. The more dislocations a metal has, the more malleable it is.
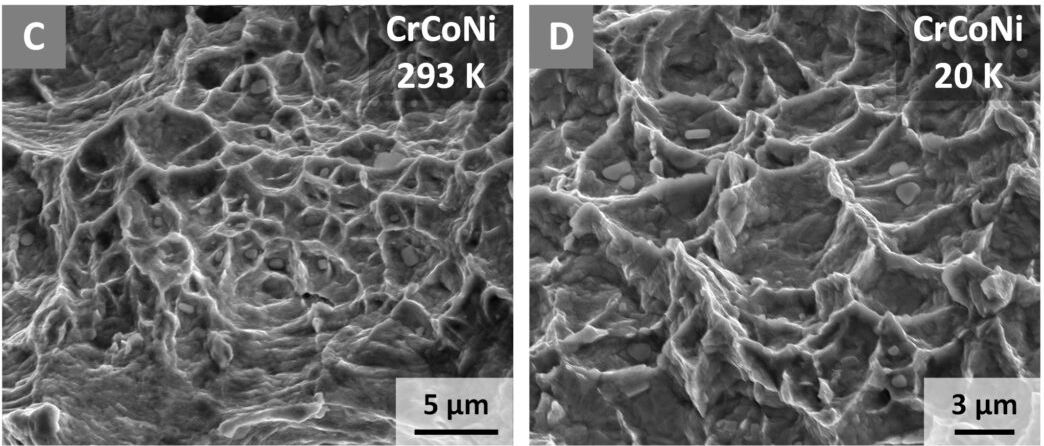
Imperfections in the metal can block the movement of dislocations; that makes a material strong. But when the dislocations are blocked, a material can fracture instead of deform, so high strength can often mean high brittleness. The researchers identified a specific sequence of three dislocation blocks in CrCoNi.
The first thing that occurs is slippage, when parallel parts of the crystal lattice slide away from each other. As a result, the unit cells no longer match perpendicularly to the slip direction.
Continued power generated nanotwins, where crystal lattices form a mirrored arrangement on either side of a boundary. When more force is applied, this energy flows into rearranging the shape of the unit cells, from a cubic to a hexagonal crystal lattice.
“As you pull it, the first mechanism starts, and then the second starts, and then the third starts, and then the fourth.” says Ritchie.
“Well, a lot of people will say, well, we’ve seen nanotwins in normal materials, we’ve seen them hatch in normal materials. This is true. There’s nothing new about that, but it’s the fact that they’re all in this magical sequence that gives us these really tremendous qualities.”
The researchers also tested CrMnFeCoNi at liquid helium temperatures, but it didn’t perform nearly as well as its simpler derivative.
The next step will be to investigate the potential applications of such a material and to find other HEAs with similar properties.
The research was published in Science.